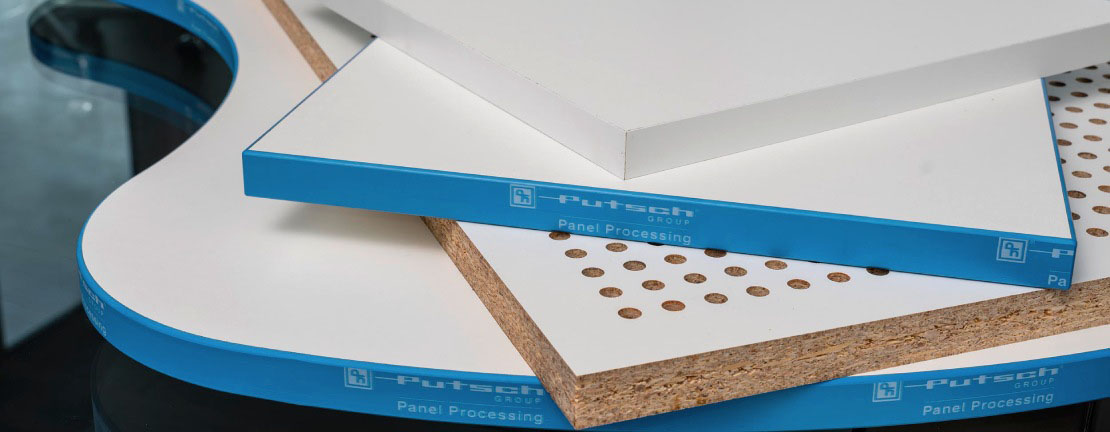
Composite materials have become a cornerstone of modern manufacturing, offering a unique combination of strength, lightweight properties, and versatility. Industries ranging from aerospace to automotive, construction, and sports equipment rely heavily on composite processing techniques to produce high-performance materials. Understanding how composites are processed is crucial for manufacturers looking to optimize production, reduce costs, and ensure high-quality products. In this article, we’ll explore the essentials of composite processing, the types of composite materials, key processing methods, and emerging trends that are shaping the future of this industry.
What Are Composite Materials?
Composite materials are engineered from two or more distinct materials that, when combined, create a new material with superior properties compared to the individual components. Typically, composites consist of a matrix (the base material) and reinforcements (fibers or particles) that provide strength, rigidity, and other enhanced characteristics. The matrix is often made from polymers, metals, or ceramics, while the reinforcement material is typically fiberglass, carbon fiber, aramid, or natural fibers.
Common examples of composite materials include:
- Carbon fiber reinforced polymers (CFRPs): Used in aerospace and automotive applications for their high strength-to-weight ratio.
- Fiberglass reinforced plastics (FRPs): Commonly used in boat hulls, pipes, and tanks.
- Concrete composites: Reinforced with fibers or other materials to enhance structural integrity.
Why Is Composite Processing Important?
Composite processing is essential because the unique properties of composite materials—such as their light weight, strength, and durability—depend on how they are fabricated. The manufacturing process significantly impacts the final product's performance, cost, and lifespan. Proper processing techniques allow manufacturers to produce composites with the required characteristics, such as improved fatigue resistance, thermal stability, and corrosion resistance.
Key Composite Processing Methods
There are various methods for processing composite materials, each suited to specific applications and types of composites. Here are some of the most common composite processing techniques:
1. Hand Lay-Up (HLU)
Hand lay-up is one of the simplest and most widely used methods of composite processing, especially for fiberglass and resin-based composites. The process involves manually placing layers of reinforcing fiber (often fiberglass mats) onto a mold, applying resin between each layer, and curing the material under heat and pressure.
Applications: Boat hulls, wind turbine blades, and automotive components.
Advantages: Low cost and flexible for small to medium production runs.
Disadvantages: Labor-intensive, less precise, and may result in inconsistent quality.
2. Vacuum Infusion
Vacuum infusion (also known as resin infusion or vacuum-assisted resin transfer molding, VARTM) is a more advanced method where the reinforcement fibers are placed in a mold, and resin is drawn through the fibers under vacuum pressure. This method is typically used for larger, more complex parts.
Applications: Automotive panels, aerospace parts, and large structural components.
Advantages: High-quality, uniform parts with reduced void content, and it’s more automated than hand lay-up.
Disadvantages: Requires more complex equipment and is typically slower than other processes.
3. Resin Transfer Molding (RTM)
Resin Transfer Molding is a closed-mold process where dry fiber reinforcements are placed in a mold, and resin is injected under pressure. The process is highly suited for high-volume manufacturing of complex parts with high fiber content.
Applications: Aerospace, automotive, and sporting goods industries.
Advantages: High precision, low porosity, and the ability to create complex shapes.
Disadvantages: High initial setup cost, which makes it more suitable for mass production.
4. Compression Molding
Compression molding involves placing preheated composite material (usually in the form of sheets or powder) into a heated mold, which is then compressed under pressure. This method is often used for thermoset composites, where the resin cures under heat and pressure.
Applications: Automotive parts, electrical enclosures, and appliance components.
Advantages: High-volume production and the ability to create intricate shapes with minimal waste.
Disadvantages: Limited to certain types of composites and requires significant upfront investment.
5. Pultrusion
Pultrusion is a continuous process where reinforcement fibers are pulled through a resin bath and then into a heated die to cure and form composite shapes. This method is typically used for producing long, straight components like rods, beams, and structural profiles.
Applications: Structural components, such as beams and columns for construction and infrastructure.
Advantages: Continuous production process, high fiber volume, and consistent quality.
Disadvantages: Limited to long, straight parts and has higher material waste during setup.
6. 3D Printing (Additive Manufacturing)
3D printing technology is making its mark in the composite industry, especially with the development of composite filaments that contain materials like carbon fiber, fiberglass, or metal powder. 3D printing allows for rapid prototyping and the production of complex geometries that are difficult to achieve with traditional methods.
Applications: Rapid prototyping, small-batch manufacturing, and aerospace parts.
Advantages: Flexibility, reduced lead times, and the ability to produce highly complex shapes.
Disadvantages: Limited by material strength and size constraints.
Key Advantages of Composite Materials
- Lightweight: Excellent strength-to-weight ratios for industries like aerospace and automotive.
- Corrosion Resistance: Ideal for marine environments, chemical industries, and construction.
- High Strength and Durability: Exceptional mechanical properties for high-performance applications.
- Design Flexibility: Molds into complex shapes, reducing additional components.
- Thermal and Electrical Insulation: Valuable in electronics and electrical power industries.
Emerging Trends in Composite Processing
- Automation: Reducing costs and improving consistency with AFP and robotic lay-up.
- Sustainability: Recycling composite waste and developing bio-based resins and fibers.
- Hybrid Composites: Combining materials for enhanced performance.
- Additive Manufacturing: Expanding possibilities for rapid prototyping.
- Advanced Resin Systems: Faster curing and improved heat resistance.
Conclusion
Composite processing plays a crucial role in the production of high-performance materials used across many industries. From aerospace to automotive, construction, and sports equipment, composites offer unmatched benefits in terms of strength, weight, and durability. By understanding the various composite processing methods—such as hand lay-up, resin transfer molding, and 3D printing—manufacturers can optimize their production processes and meet the growing demand for advanced materials.
Whether you're involved in designing aircraft, building infrastructure, or creating consumer products, staying informed about the latest advancements in composite processing can help your business achieve better performance, lower costs, and superior product quality.