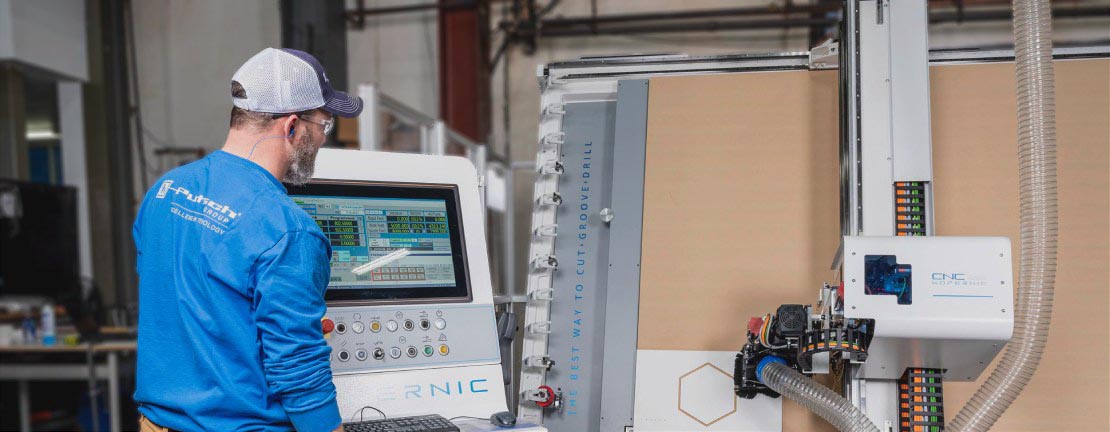
In today’s fast-paced manufacturing environment, precision, speed, and efficiency are paramount. One of the key innovations that has transformed the manufacturing industry is the CNC Machine Center. These advanced machines combine the versatility of CNC (Computer Numerical Control) technology with multi-functional machining capabilities to offer manufacturers a significant competitive edge.
What is a CNC Machine Center?
A CNC Machine Center is a sophisticated machine tool that automates the process of drilling, milling, and other machining operations using pre-programmed computer software. Unlike traditional machine tools that require manual operation, CNC machine centers are designed to perform a wide range of tasks with high precision and minimal human intervention. They are capable of producing complex parts with tight tolerances, making them invaluable in industries such as aerospace, automotive, electronics, and medical device manufacturing.
The term "machine center" generally refers to a machine that incorporates multiple axes of movement, enabling it to perform multiple machining functions (like drilling, turning, and milling) without the need to reposition the part manually. This capability streamlines production and increases efficiency, reducing setup time and the potential for human error.
Types of CNC Machine Centers
- Vertical CNC Machine Centers: In these machines, the spindle is oriented vertically. They are ideal for operations such as drilling, boring, and milling, and are commonly used for machining small to medium-sized parts. Vertical machine centers are well-suited for industries that require intricate work on smaller components.
- Horizontal CNC Machine Centers: These machines have a horizontal spindle orientation, which makes them perfect for handling large, heavy workpieces. Horizontal CNC machine centers are typically used in industries like automotive and aerospace, where high-volume, high-precision parts are produced.
- Multi-Axis CNC Machine Centers: These machines offer greater flexibility by incorporating additional axes of movement (typically 5 or more). Multi-axis CNC machine centers can perform more complex operations such as contouring and multi-directional cutting. These centers are essential for industries where intricate and high-tolerance parts are needed, such as the aerospace and medical fields.
- Turn-Mill CNC Machine Centers: These machines combine both turning and milling capabilities in a single setup. They are designed for parts that require both turning and milling operations, eliminating the need for multiple machines and setups, thus reducing production time and improving precision.
Benefits of Using CNC Machine Centers
- Precision and Accuracy: The primary advantage of CNC machine centers is their ability to produce parts with incredible precision. These machines are controlled by computer software, which translates designs into exact movements of the machine tool. This results in high-quality parts with tight tolerances, often within microns.
- Increased Efficiency and Speed: CNC machine centers automate many of the processes that would traditionally be done manually. This leads to faster production cycles and less downtime between jobs. The reduction in human error also means that parts can be produced in larger quantities without sacrificing quality.
- Versatility: A CNC machine center’s ability to perform various machining operations in one setup is a key advantage. Whether it’s drilling, tapping, milling, or even turning, these machines can execute a wide range of tasks without the need to switch between multiple machines. This versatility reduces production costs and simplifies workflows.
- Cost Savings: While the initial investment in CNC machine centers can be high, the long-term cost savings are significant. Reduced setup times, fewer errors, and less waste all contribute to lower production costs. Additionally, CNC machine centers are often capable of running around the clock, further increasing productivity.
- Automation and Reduced Labor Requirements: CNC machine centers can operate autonomously once set up, reducing the need for skilled manual labor. Operators are still required to load materials and monitor the machines, but the reliance on skilled machinists is much lower compared to traditional manual machining methods.
Applications of CNC Machine Centers
- Aerospace Industry: The aerospace industry demands extremely high precision and reliability. CNC machine centers are used to manufacture complex components for aircraft, satellites, and other aerospace applications. Parts such as turbine blades, fuselage components, and structural elements are all produced using CNC technology.
- Automotive Manufacturing: From engine parts to chassis components, CNC machine centers are essential in the automotive industry. Their ability to handle high-volume production and produce intricate parts with tight tolerances makes them ideal for automotive manufacturing.
- Medical Devices: In the medical field, precision is critical. CNC machine centers are used to manufacture medical components such as surgical instruments, implants, and diagnostic devices. These parts often require fine details and must meet stringent regulatory standards, making CNC technology indispensable.
- Electronics: The electronics industry also benefits from the precision and speed of CNC machine centers. From small connectors to complex circuit board components, CNC machine centers enable manufacturers to produce parts with high accuracy and in high volumes.
Conclusion
CNC Machine Centers are the cornerstone of modern manufacturing, offering unmatched precision, efficiency, and versatility. These advanced machines have transformed industries across the globe, from aerospace to automotive and beyond, enabling manufacturers to meet growing demands for high-quality, complex parts. As technology continues to evolve, the role of CNC machine centers will only expand, driving further innovation and growth in the manufacturing sector.
By investing in CNC machine centers, manufacturers can not only increase production speed and reduce costs but also gain a competitive edge in an increasingly globalized market. Whether you're involved in prototyping or mass production, these machines are an essential tool for achieving success in the modern manufacturing landscape.